The Different Types of Sheet Metal Fabrication Explained
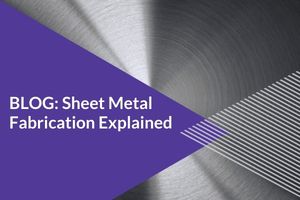
April 13, 2022
Sheet metal fabrication is a general term for the process, but there is more than one type of sheet metal fabrication, each with their own strengths, weaknesses, and uses. In this piece we set out to explain the differences between the different forms of sheet metal fabrication, the different metals used, and how to choose the right sheet metal for your project.
What You Need to Know About Sheet Metal Fabrication
Sheet metal fabrication is the manufacturing process by which sheet metal is processed to create parts and shapes. Sheets of metal are coerced into different shapes using a range of techniques including bending, rolling, punching, cutting, and welding to create new forms.
Occasionally this is the end of the process, and the resulting metal shape is the finished article. But most of the time products created by sheet metal fabrication go on to become a component in a larger product.
The Different Types of Sheet Metal
It’s important to choose the right sheet metal for your project depending on the end use. Each has unique characteristics that will make it more, or less suited to job at hand.
For example, what are the most important aspects of the metal for your project?
- Does it need to be robust?
- Will it be subject to heavy wear and tear?
- Does it need to be malleable?
- Will it be subject to extremes of heat or cold?
- Does it need to be corrosion resistant?
- Will it be welded to other parts?
- Will the part require a cosmetic finish?
Stainless Steel
Stainless steel is a common sheet metal used in a wide range of applications across many industries. From kitchen appliances to parts designed for use in airplanes, stainless steel can be found just about anywhere you care to look.
The Benefits of Using Stainless Steel
Stainless steel is a popular choice for contract manufacturing due to its unique properties. It is easy to weld, strong, hygienic and corrosion resistant. Stainless steel has a more pleasant aesthetic than many of its counterparts, which makes it a great choice for application where it can be seen, for example in its use in architectural finishes, kitchen appliances and equipment casings etc.
Stainless steel is also known for its ability to withstand very high temperatures. Another common use for it is in kitchen equipment such as pots and pans, and even as part of or all of the kitchen itself. Thanks to its natural hygienic properties, most surfaces and equipment used in commercial kitchens are usually made from stainless steel. This includes work surfaces, ovens and hobs, flues and vents, cutlery and more. The same applies to medical environments and equipment where stainless steel is used in the surgical instruments being used right through to implants and prosthetic components.
Carbon Steel
Carbon Steel often referred to as CR4 mild steel is an iron-carbon alloy available in low/mild, medium and high carbon steel. It is used in a wide range of applications, many of them on a large scale such as for use in buildings, bridges, and pipelines.
The Main Advantages of Using Carbon Steel
Carbon steel is known for its malleability and environmentally friendly attributes. It is easily recycled making it an attractive choice to any industry looking to reduce their impact on the environment, or to produce items which help the end user do so. Carbon steel is a popular choice for contract manufacturers due to its workable nature, making it easy to handle and fabricate. Available in a range of hardness and strength levels, carbon steel can be used for a wider range of contract manufacturing and fabrication applications than most other metals.
Tool Steel
Tool steel is a particular carbon and alloy steel popular in the manufacturing of tools.
There are six distinct types of tool steel:
- Water hardening - requiring to be quenched with water
- Cold work - for use on low temperature materials
- Shock resisting - to bear higher levels of shock at all temperatures
- High speed - commonly used in cutting tools
- Hot work - for use on high temperature materials
- Special purpose - includes low alloy (L type), plastic mould (P type) and F-type extra wear resistant
When Should Tool Steel Be Used in Contract Manufacturing?
Tool steel is not only the best choice for contract manufacturing tools, but it can also be the optimal choice of metal in a range of other sectors including healthcare and mould work. Speak to your contract manufacturer about the best choice of metal for your fabrication project.
Galvanized Steel
Regular steel will rust when exposed to the water or moisture. Galvanised steel is ordinary steel which has been coated in zinc to create a corrosion resistant layer, allowing it to be used in outdoor settings and where exposure to damp or wet is expected.
The Benefits of Using Galvanized Steel
The main benefit of galvanised steel is its ability to withstand damp or wet environments, extending both the possible uses and the life of the material. It is a cost-effective material and offers long and reliable performance. Galvanised steel is low maintenance too, making it a firm favourite for metal fabrication contract manufacturing.
Galvanising provides a tough and permanent coating to the steel which is easy to clean, robust and enduring. It is also lower in cost when compared to other types of coating however, in general Stainless Steel is more resistant to corrosion than galvanised steel and is easier to work
Aluminium Steel
Aluminium steel is sheet steel which is coated in aluminium, or an aluminium-silicone alloy. It is commonly used in applications involving exposure to high temperatures and damp environments. It can be found as part of kitchen equipment, barbeque set ups, exhaust systems and water heaters.
What are the Benefits to Using Aluminium?
Contract manufacturing projects based around automotive and cookery/kitchen-based products will often use aluminium steel. Maintaining a high strength and longevity in corrosive environments, plus its low price compared to high-alloy steels makes it an effective and economical choice for sheet metal manufacturing projects.
Why Stainless Steel Is One of The Best Metals for Contract Manufacturing
Stainless steel combines the features and benefits of a number of other metals commonly used in contract manufacturing and is a strong and cost-effective material to work with. Offering a wide range of applications from hospitality to medical and industrial to safety, stainless steel is a great choice for many contract manufacturing projects.
The key benefits of using stainless steel in contract manufacturing include:
- Ease of manipulation - easy to cut, shape and weld
- Impact resistance - high strength and durability
- Heat resistance - for use in high heat environments and for fire safety
- Corrosion resistance - for longevity and durability
- Aesthetic appeal - clean, modern, hygienic surface with aesthetic appeal
- Cost - cost effective sheet metal for use in contract manufacturing
How to Know Which Type of Sheet Metal Fabrication Is Needed for My Project?
The most suitable sheet metal for your contract manufacturing project depends on a number of factors including design, purpose, environment and budget. If you are unsure which sheet metal is best for your application, speak to our contract manufacturing experts today for help and advice on your project choices.
How Dudley Industries Can Help with Your Next Sheet Metal Project
Dudley Industries has an in-house team of experts who can help with your next contract manufacturing project no matter how big or small. With over 70 years in contract manufacturing and ISO 9001:2015 accreditation, your project is in safe hands with Dudley Industries.
Call our team today on 01253 738311 or contact us via the enquiry form HERE